Cutting-edge CFD modelling
and world fuel expertise
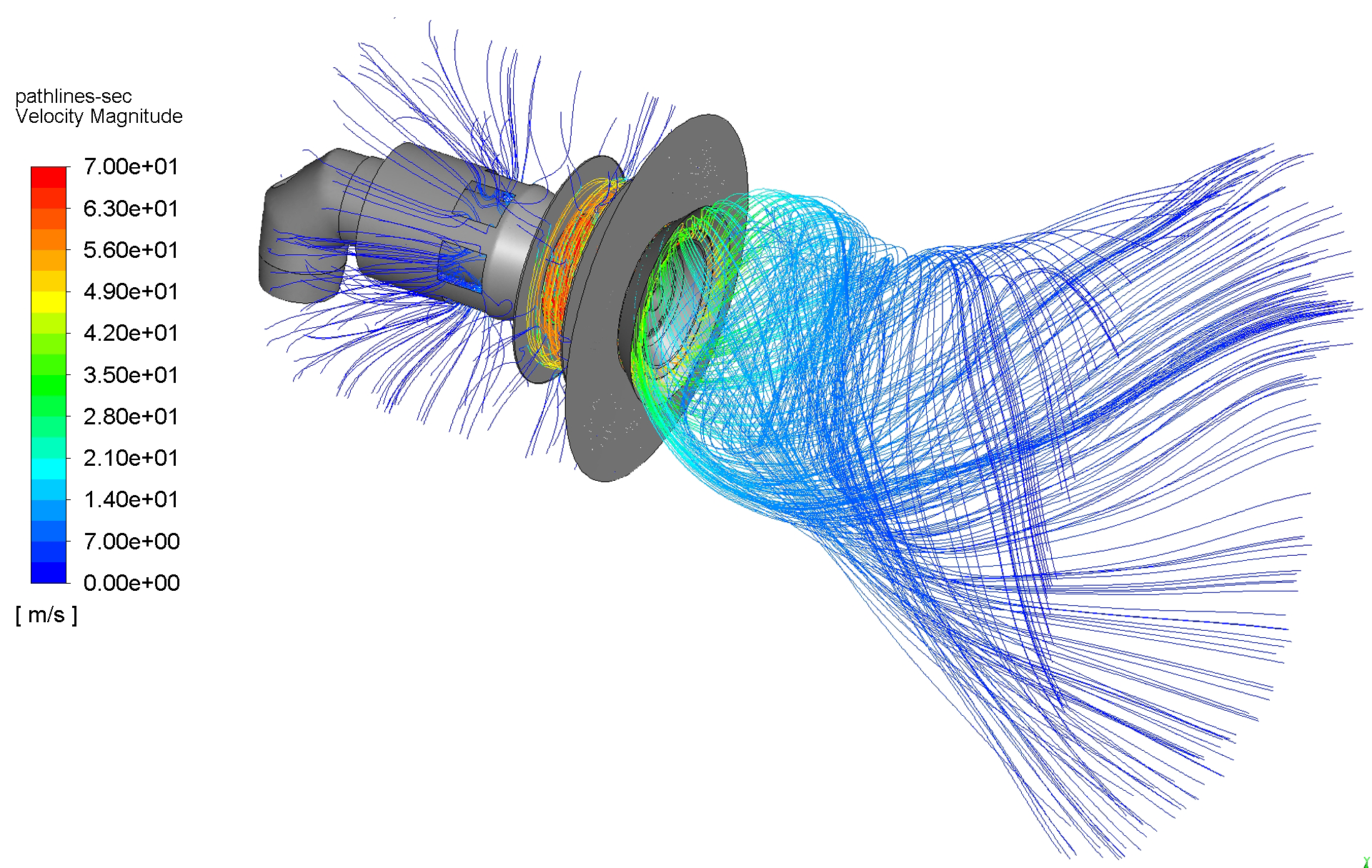
RJM has experience modelling a wide array of boiler types, sizes, firing system designs and fuel types
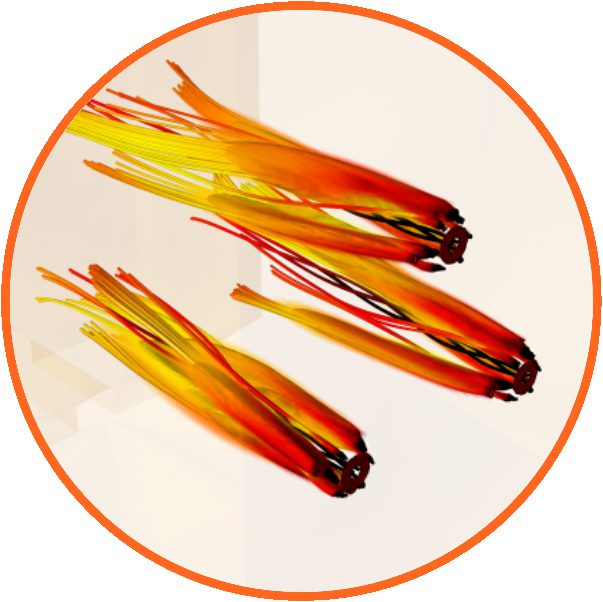
natural gas
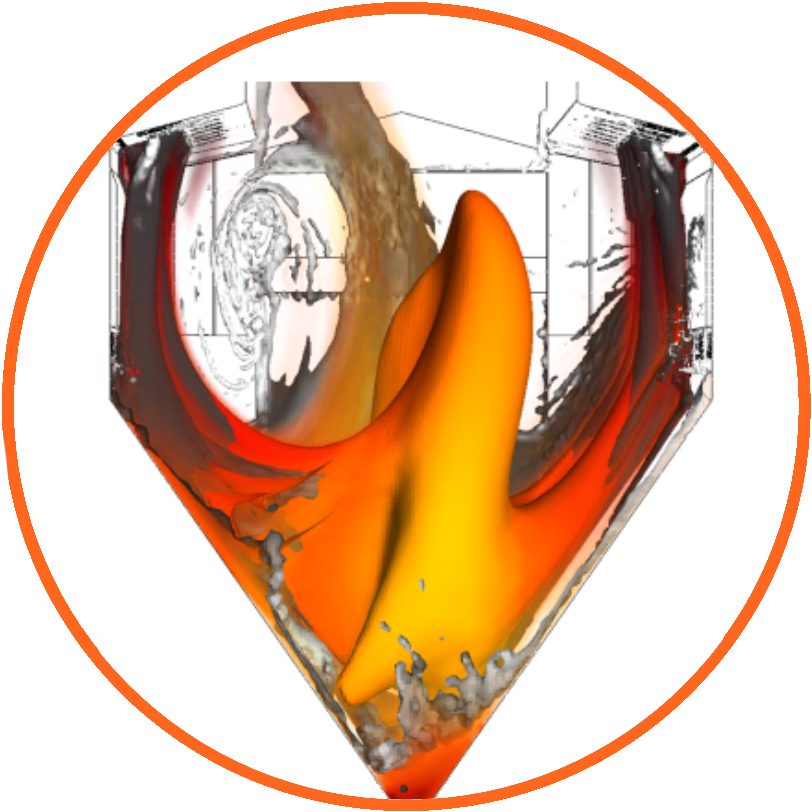
anthracite
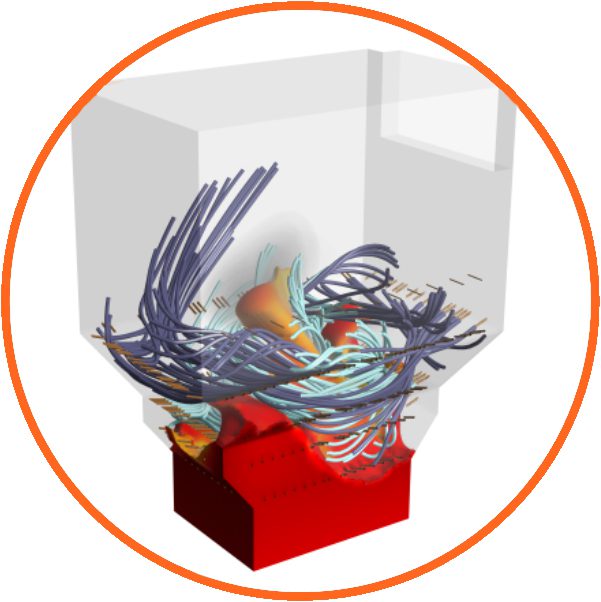
coal and biomass

bituminous coal and oil
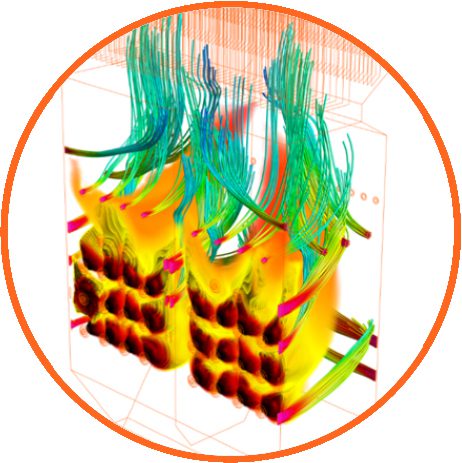
sub-bituminous coal
Harnessing CFD to deliver performance improvements
Today, RJM continues to push at the boundaries of combustion CFD modelling to resolve the most complex combustion challenges, including helping its customers explore the use of new, lower-carbon fuels. Through continued investment in CFD programming and its in-house team of CFD engineers, RJM is able to achieve exceptionally low NOx emissions, at levels that were previously thought impossible through primary measures alone.
RJM also uses CFD to facilitate other combustion improvements including CO, unburnt carbon, temperature imbalances, slagging and fouling predictions.
RJM’s proprietary CFD modelling process follows a well-proven framework.
+ Discover
The final Upgrade Model provides the details of the solution required to meet the customer’s performance objectives and gives a reliable prediction of the performance to be expected. This in turn enables the customer to make an informed investment decision about proceeding with the proposed upgrade.
With over 40 years’ CFD experience, RJM is so confident in the results of its modelling that it uses CFD to guarantee the performance of its proposed solutions.
Close X
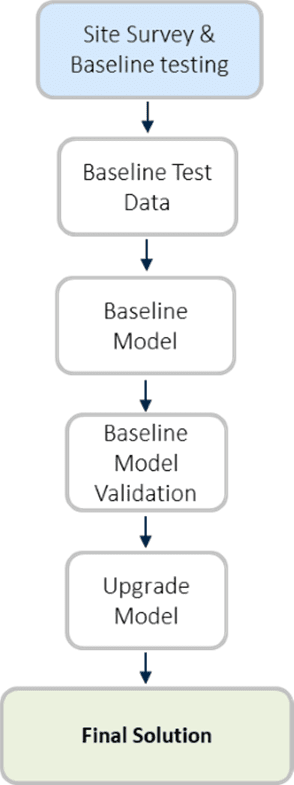
Unrivalled knowledge of world fuels and fuel behaviour is the cornerstone of RJM’s ability to solve complex combustion issues

Understanding fuel
characterisation
+ Discover
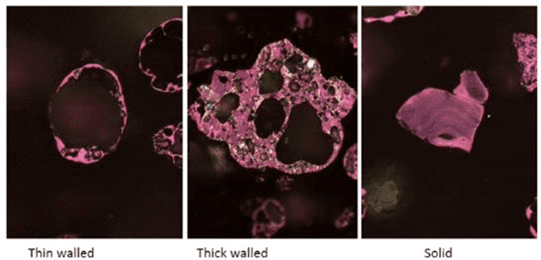
RJM’s Fuel Assessment Services
This includes an add-on cost model and shows the true value of a fuel, relative to a ‘reference’ fuel. RJM’s fuel assessment service can be coupled with a combustion optimisation programme to deliver maximum plant benefits.
Combining its knowledge of combustion and fuels, RJM can offer a wide range of bespoke and customisable fuel assessment services to help customers optimise their fuel diet and fuel management strategies, taking into account plant design, performance and operational limitations.
Where plants are considering a fuel switch, such as a coal plant co-firing with biomass or a biomass plant introducing a new waste stream fuel, RJM can offer a full plant conversion service, including risk assessment.
RJM uses Drop Tube Furnace testing to evaluate fuel particle combustion behaviour and to calibrate our proprietary CFD models for each project.
Close X
RJM’s Fuel Assessment services include an add-on cost model – this shows the true value of a fuel relative to a ‘reference’ fuel. RJM’s fuel assessment service can be coupled with a combustion optimisation programme to deliver maximum plant benefits.
Combining our knowledge of combustion and fuels, RJM offers a wide range of bespoke and customisable fuel assessment services to help customers optimise their fuel diet and fuel management strategies, taking into account plant design, performance and operational limitations.
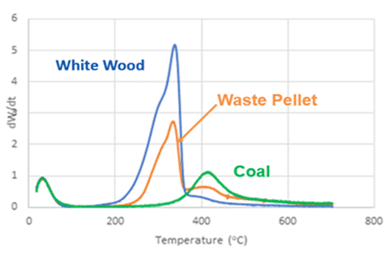
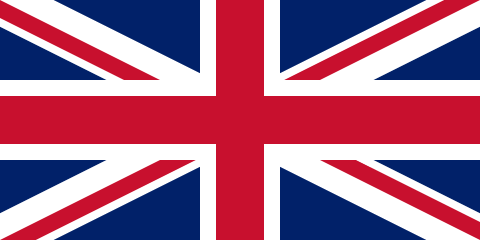
Case study - Kilroot
Exploiting advanced CFD modelling to reduce NOx to 250mg/Nm³
RJM’s patented SUFA system now delivering additional NOx performance
Discover +
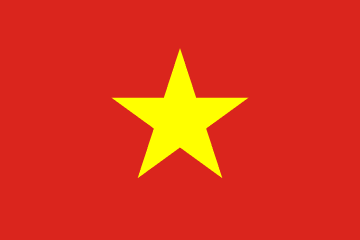
Case study - AES-VCM Mong Duong II
Exploiting advanced CFD modelling to resolve a range of issues
RJM’s unique approach improved combustion and flame stability
Discover +
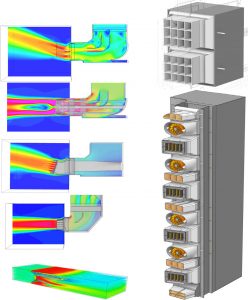
For Kilroot, sophisticated CFD modelling of every nozzle and damper has enabled RJM to “fill in the gaps” of the on-site instrumentation
Combustion CFD models are essentials for capturing thee incredible complexity of T-fired boilers, where individual jets of air can have a significant impact on local NOx production and impingement on wall tubes. These models are essential for fully capturing the impact of the proposed upgrades, and with RJM’s new High-Performance Cluster (HPC) supercomputer, these six million cell models, can be run in 12-18 hours rather than days, allowing for rapid development of solutions. At Kilroot, this has been used to develop an upgrade solution to utilise RJM’s patented Separated Under-Fire Air (SUFA) system to deliver air through the centre of the fireball and reduce thee amount of air injected through conventional means. This work strives to reduce NOX through primary measures only, whilst also reducing unburnt Carbon in Ash.
Example of RJM’s detailed CFD work to optimise its SUFA solution
Close X
The resulting improvements have completely met our expectations.”
Kevin Pierce, Plant Manager, AES-VCM Mong Duong II, Vietnam
Find out how RJM resolved these issues…
RJM was tasked with carrying out a series of engineering work packages to:
- Determine the root-cause of the combustion and boilers issues
- Design a cost-effective combustion improvement solution
- Supply the combustion system upgrades required
- Meet the project’s objectives of improved performance, reliability and efficiency
- Improve the plant’s operability by improving the reliability of the flame monitoring system
- Reduce Heavy Fuel Oil usage during start-up, shut-down and as a combustion support
Research & Analysis
Firstly, RJM performed a unique suite of integrated work packages, designed to fully characterise the system and the fuel. They included:
• Site Surveys: For data collection & analysis, including visiting other plants with the same system design
• Plant Testing: Including slag monitoring and analysis
Isothermal CFD Modelling: For all windboxes and ductwork, to determine air flow splits and distribution
• Physical Modelling: Analysing of the cyclones, to determine the PA/PF flow splits and distribution
• Coal Characterisation: Using advanced laboratory testing and proprietary modelling techniques
Building the CFD models
Each of these work packages produced critical input data for the CFD model, enabling RJM to produce a half-furnace combustion CFD model that would provide reliable and accurate results and predictions. The CFD model results were then validated through a series of comprehensive site tests, analysis and observations, before RJM utilised the model to custom-design a set of cost-effective modifications to the existing combustion system. These modifications included:
• Cyclone Deflectors, Orifice Plates and Flow Straighteners
• Tertiary Air Vanes
• Secondary Air Nozzle Plates
• Ductwork Turning Vanes & Distribution Devices
Benefits to the plant
The results included substantially improved combustion performance and flame stability. This in turn enabled AES-VCM to remove a large portion of the furnace refractory to reduce slag-build up and mitigate large slag falls, which resulted in a significant improvement in unit reliability, to a point today where combustion related unit trips are almost unknown.
Working directly with site engineers, new optimum mill firing configurations were also devised and implemented and these have resulted in a significant improvement in combustion efficiency, with a large reduction in carbon in fly ash.
Final Boiler NOx: | 550ppm – 600ppm | (10-15% reduction) |
Final Carbon Ash: | 3.0 – 5.5% | (30-40% reduction) |
Improving performance and reliability at AES-VCM Mong Duong II has been one of the most complex assignments ever tackled by RJM.
Looking to the future
RJM is still working closely with the in-house team at the power station and continuing to deliver a programme of incremental improvements across the plant. Much of this has been achieved through remote monitoring of the plant’s DCS by RJM’s engineers in the UK.
The Master Firing Trip System that RJM developed and refined to optimise furnace safety, is now undergoing a thorough assessment programme, also via remote monitoring.
“RJM has been a trusted partner in our efforts to improve combustion and unit reliability at our 1,200MW Mong Duong II facility in Vietnam. RJM’s engineering strengths, combustion modelling and experience has helped guide us in quickly making the proper decisions on needed modifications. The resulting improvements have completely met our expectations.”
Kevin Pierce, Plant Manager, AES-VCM Mong Duong II, Vietnam
Manufacturer | Doosan Heavy Industries |
Type | Utility |
Capacity | 1,912,473 kg/h |
Fuel | Anthracite Coal |
Burners | Doosan Cyclone Slot Burners with Thermal Input Biasing 65MWth each |
Firing Arrangement | Downshot ‘W’ Fired / Arch-Fired – 24 burners |
Close X
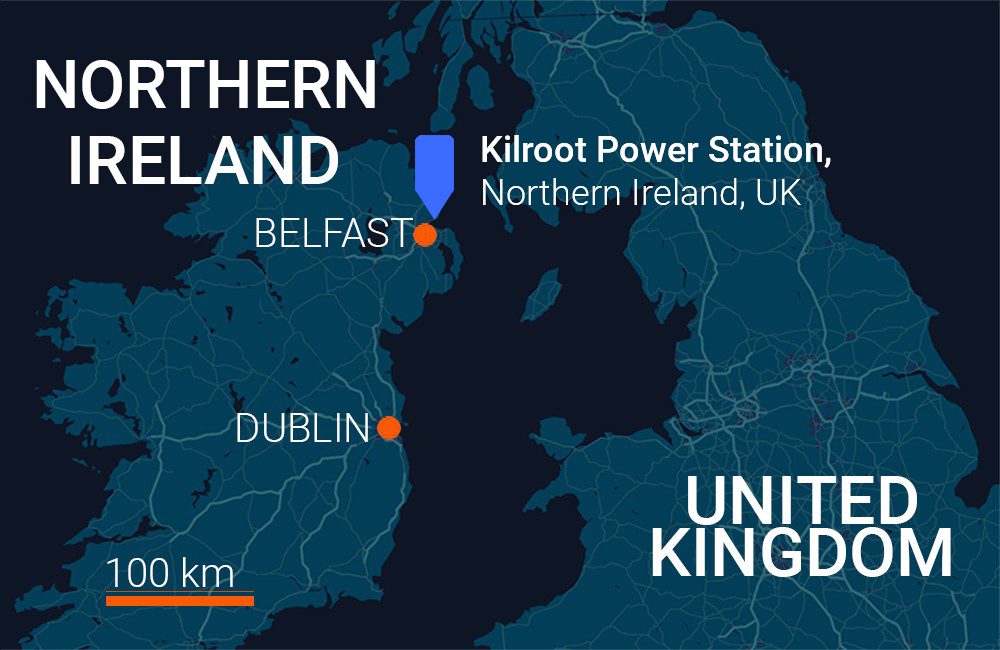
Kilroot Power Station, Northern Ireland, UK
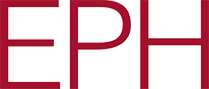
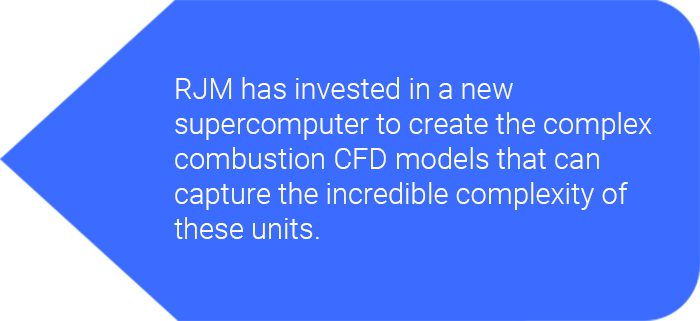
RJM has invested in a new supercomputer to create
the complex combustion CFD models that can
capture the incredible complexity of these units.
Projects
FEED study to convert a PF coal plant to fire a waste-derived pellet
Wales
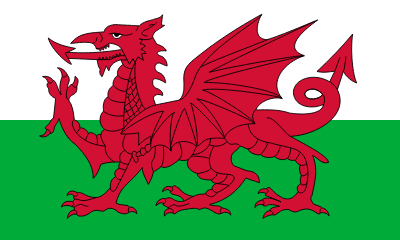
SIMEC, Uskmouth
Key challenges
To support the world-first conversion of a front wall-fired PF coal plant to fire a waste-derived energy pellet consisting of 50% biogenic material and 50% plastic not suitable for recycling.
Resolving a range of operational problems at a 28Mwe fluidised bed plant
Country
UK
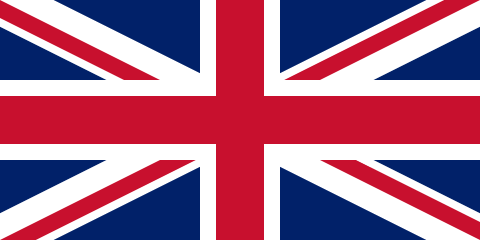
Energy Works Hull
Key challenges
This 28MWe fluidised bed gasification plant, firing multiple solid fuels was experiencing various operational problems. Also, due to over-reliance on its secondary support fuel, it did not meet the criteria to qualify for the Contracts for Difference low carbon subsidy scheme, which seriously impacted on the financial viability of the plant.
€76m EU-funded NOx reduction project
Country
Kosovo
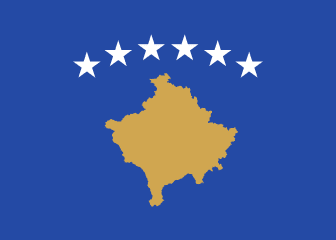
Kosovo B, Pristina
Key challenges
As part of Kosovo’s accession planning to join the European Union, its 680MWe lignite-fired power station, Kosovo B needs to be brought up the latest EU standards.
Project to reduce NOx and return plant to full output
Country
Eire
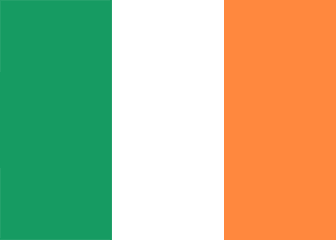
SG6, Irving Oil
Key challenges
The main challenge for RJM was to reduce the amount of flame impingement on the boiler tubes, as this was preventing the plant from operating at full power. In addition, it had to be achieved in a way that ensured NOx emissions remained below the 250mg/Nm3 threshold.