RJM’s IMPULSE® Cleaning System
is revolutionising online cleaning
The IMPULSE Cleaning System significantly reduces the build-up of fused ash deposits and enables plants to operate longer campaigns with reduced downtimes
IMPULSE Cleaning at Mach 5
RJM is now selling the innovative and highly-effective IMPULSE Cleaning system exclusively in Europe. This technology has already been deployed successfully on over 350 units across the USA.
Click here for IMPULSE video
How it works...
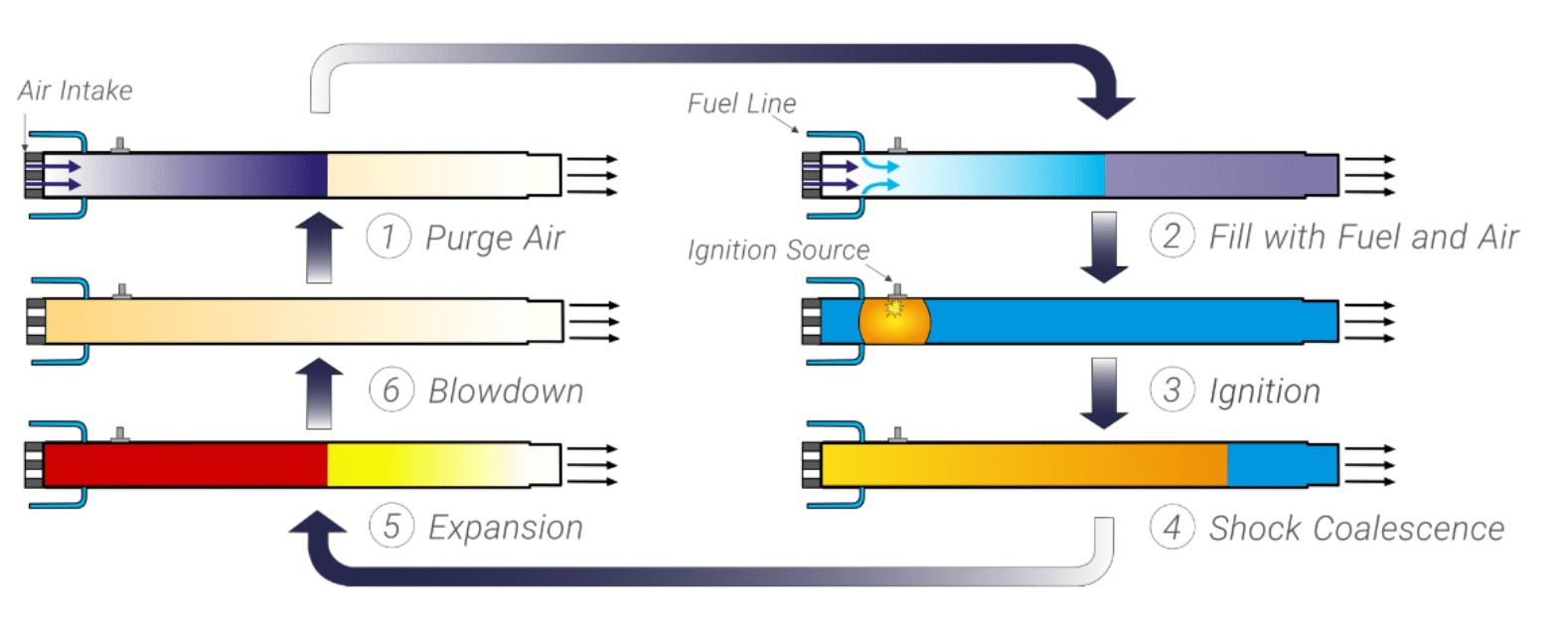
- Cyclic combustion event creates supersonic impulses
- Injection of fuel and air into mixing chamber followed by ignition and combustion
- Shockwave is result of the acceleration of a flame to supersonic speeds over short distance and time
Areas of deposition between the boiler tubes is successfully removed by the supersonic impulses
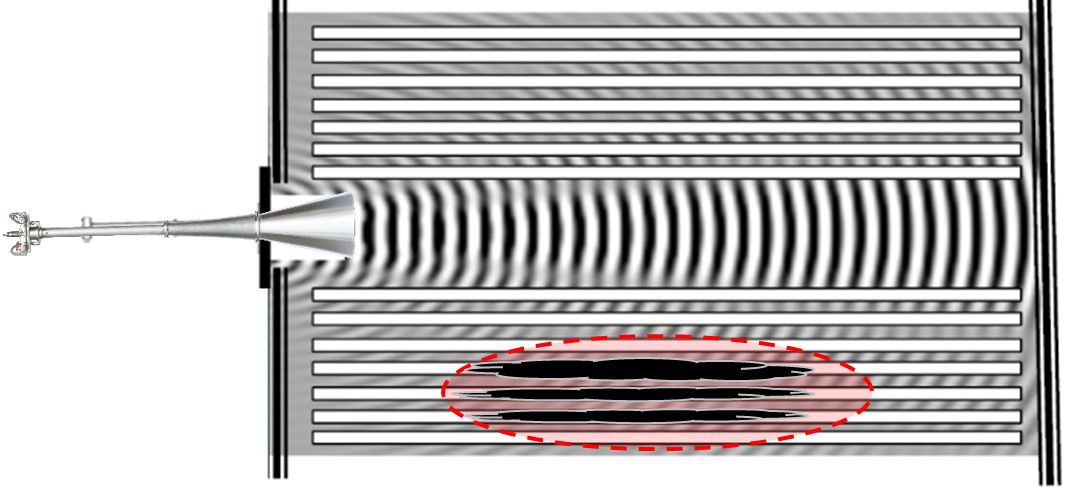
- Intense cleaning waves approach tube surfaces, encompass tube surfaces, transition around to back side, reconnect, and continue travelling.
- Non-Line-Of-Sight Cleaning
- Deep Penetration throughout tube bundle
- Non-erosive

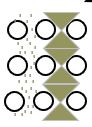
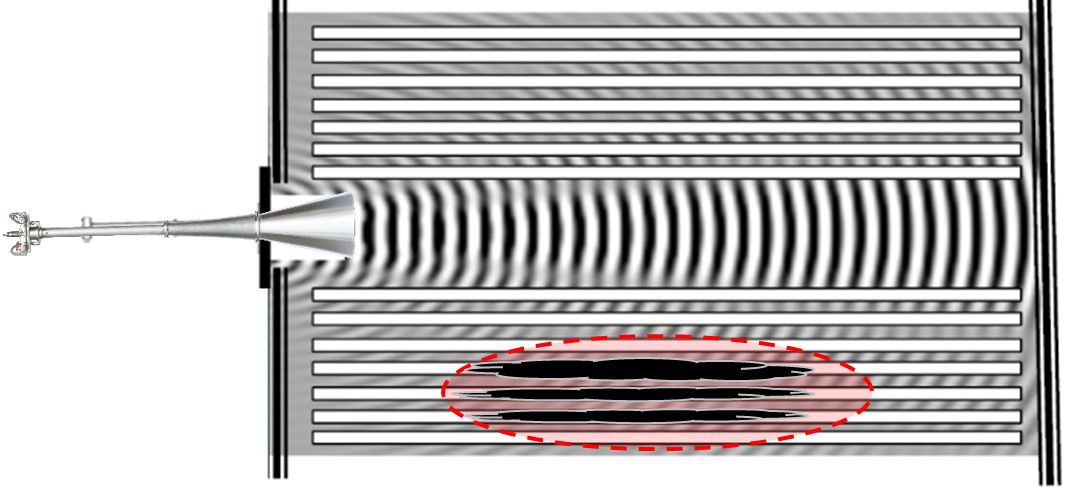

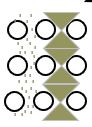
- Intense cleaning waves approach tube surfaces, encompass tube surfaces, transition around to back side, reconnect, and continue travelling.
- Non-Line-Of-Sight Cleaning
- Deep Penetration throughout tube bundle
- Non-erosive
Key advantages of IMPULSE Cleaning:
- Effective and efficient on-line cleaning system
- No erosion or damage to heat transfer surfaces
- Low Opex and maintenance; innovative design avoids moving parts
- Minimal intrusion into boiler means small installation footprint and low installation cost
- Does not scavenge plant steam, therefore no reduction in exported power
- Negligible recoil from proprietary detonation technology
- Non line-of-site cleaning; better coverage than sootblowers
- Significantly less expensive capital cost and lower operational costs than its competitors
- Suitable for all boilers, all sizes, all combustion technologies and all fuels
- Proven technology with over 340 installations in the USA
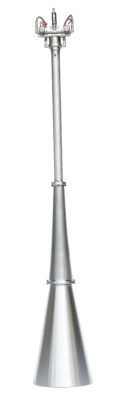
Harnessing Supersonic Shockwaves to Deliver Optimal Cleaning
Pulse detonation cleaning technology employs a rapid series of supersonic shockwaves.
Each high velocity shockwave is characterised by a high-density front, followed by an ultra-low pressure behind the shock that generates a vacuum, which in turn creates a substantial trailing edge vortex or eddy current.
The repeated combination of ultra-high and ultra-low pressures causes trailing eddy currents to form which effectively dislodge and sweep away stubborn deposits on the front and opposing faces of the heat transfer tube surfaces.
In addition, wherever shock waves are reflected off hard surfaces, this further improves the effectiveness of the cleaning.
A System Consists of:
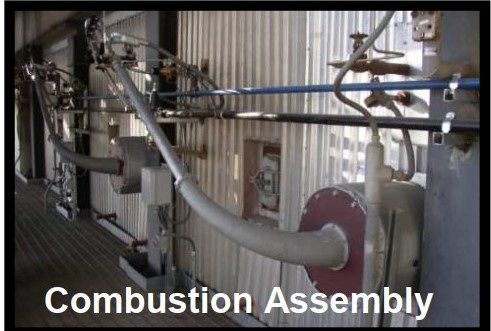
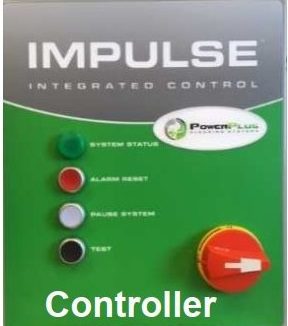

Our Customer Operations in the USA
Facility | Fuel | Plants | IMPULSE Units |
---|---|---|---|
Utility | Coal / Peat Coke | 49 | 198 |
EfW | MSW Mass Burn | 7 | 59 |
EfW | Refuse Delivered Fuel | 1 | 6 |
Co-Gen | Biomass | 5 | 13 |
Industrial | Waste Heat Recovery | 11 | 74 |
Total |
73 |
350* |
* As at September 2024
Case-study: Large municipal utility in Florida
- 2 x 297.5MW Circulating Fluidised Bed Units
- Firing Coal, Petcoke and Refuse Derived Fuels
- Post IMPULSE Cleaning installation, Unit 1 now delivering over $2.24 million annual reduction in Opex and Unit 2 an Opex reduction of over $2.28 million (300 days at full load). Unit 2 also with an improved heat rate of 2.5%.
- Following the impressive results of the first IMPULSE Cleaning installation in autumn 2020, an additional 14 units were installed on Unit 1 in April 2022.

The results were dramatic. The plant personnel had never seen the boiler looking so clean after a year of operation. The IMPULSE system has maximised production and allowed us to operate both boilers for the entire nine month processing season without the need for a forced outage.
Jeff Kava,
Western Sugar
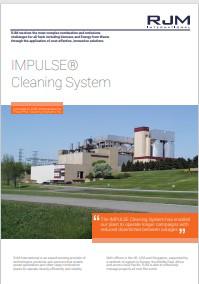
Click here to download the IMPULSE Cleaning Brochure
Projects
RDF | Full plant performance upgrade
UK
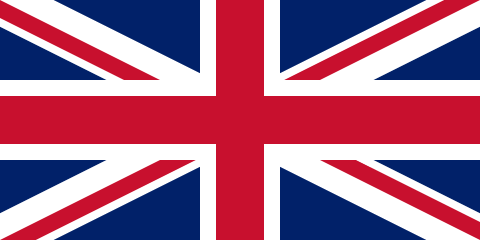
Energy Works Hull
Key challenges
This 28MWe fluidised bed gasification plant, firing multiple solid fuels was experiencing various operational problems. Also, due to over-reliance on its secondary support fuel, it did not meet the criteria to qualify for the Contracts for Difference low carbon subsidy scheme, which seriously impacted on the financial viability of the plant.
Waste wood | Full plant performance upgrade
UK
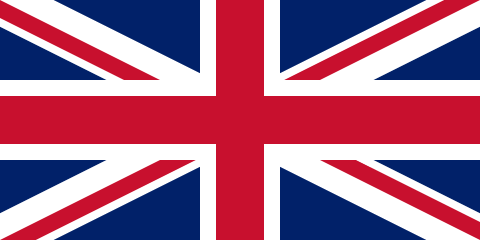
Ince Bio Power
Key challenges
The plant was experiencing a number of operational issues that impacted negatively on performance, including excessive slagging, fouling and corrosion.
Waste | NOx abatement strategy
UK
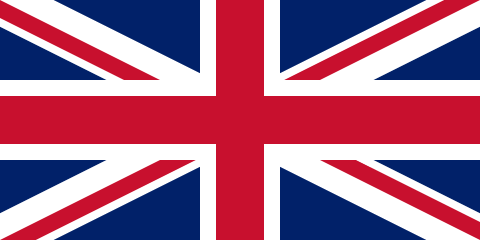
Tradebe, Fawley
Key challenges
This rotary kiln firing system processes a range of hazardous and medical waste streams and the plant operator initially tasked RJM to carry out a NOx abatement study.
Coal | Multi-element project to improve reliability
Vietnam
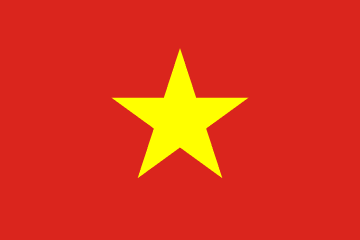
Mong Duong II
Key challenges
Firing a local anthracite coal, both boilers on this newly-built plant suffered severe slag build-up resulting in frequent and large slag falls and unstable combustion, causing frequent loss of flame and unit trips.
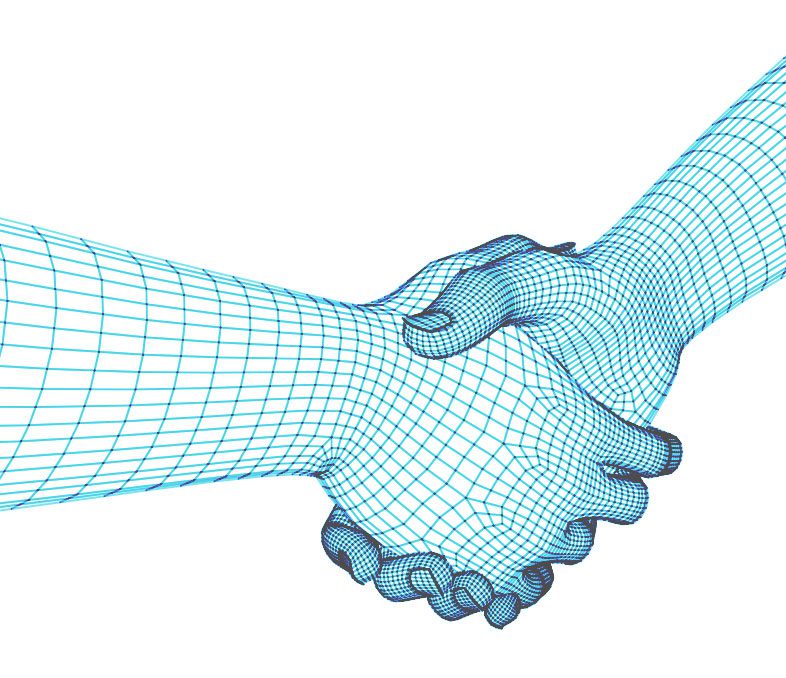
Partnership in action
RJM appointed HKL Global to act as its
agent in the Chinese industrial burner
market in 2016. The two companies have
been working closely together since then,
building up sales of the CleanAir Burner™
within Beijing and now rolling out this unit
into greater China.