Waste to Energy solutions for
old and new plant
The world is drowning in plastic waste. RJM is exploring how this waste can be used as the core component of a “new generation” fuel. The ambition is that this fuel can be fired in re-tasked power stations to deliver reliable, affordable, low-emission and low-carbon power worldwide
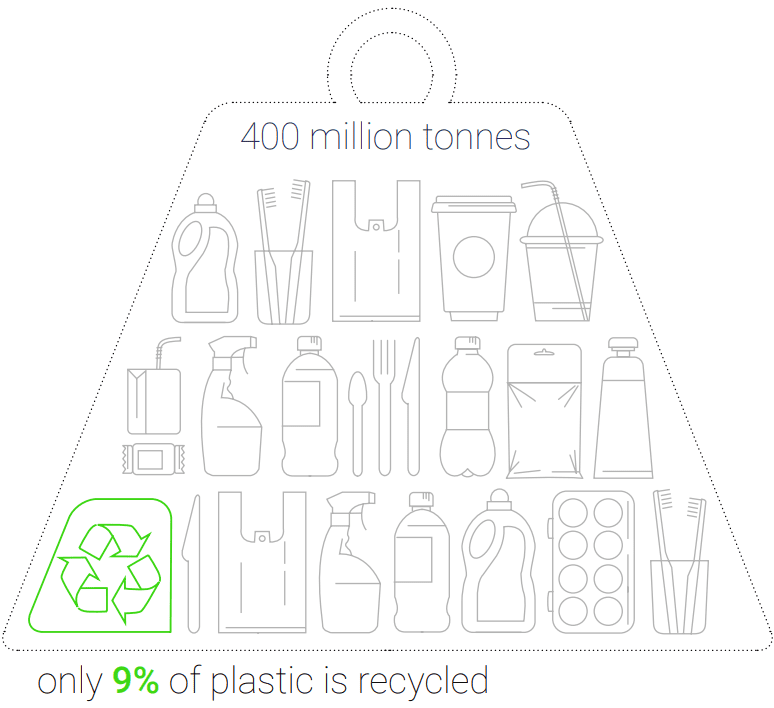
400 million tonnes
of plastic are produced
each year
91%
is not recycled
Enough waste to power all 28 million homes in the UK for over 18 months
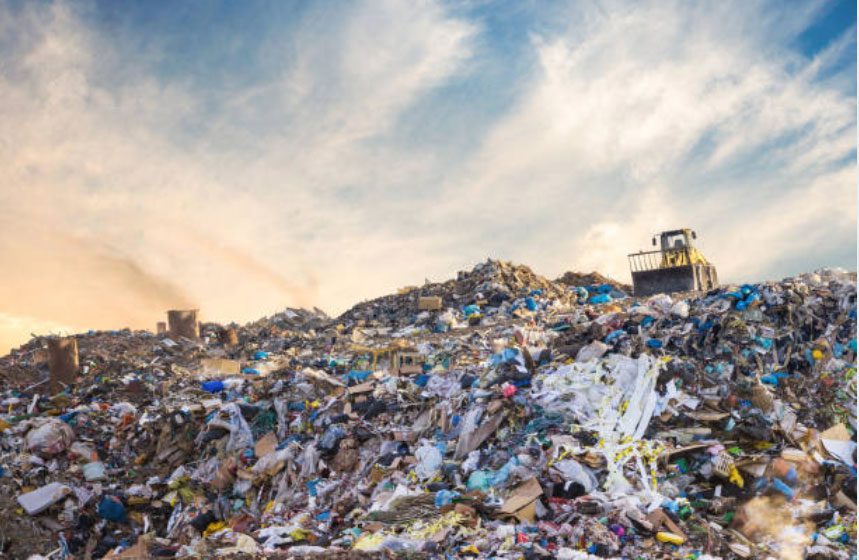
Case study – SIMEC Uskmouth Power Station
Pioneering low carbon energy from waste plastic
Re-tasking a pulverised fuel coal-fired plant
for 21st century low carbon generation
RJM’s pioneering work is helping to tackle the big issue of non-recyclable plastic waste management and harnessing it to deliver low carbon, baseload power into the grid. This important work will form the basis for the conversion of similar plants worldwide.
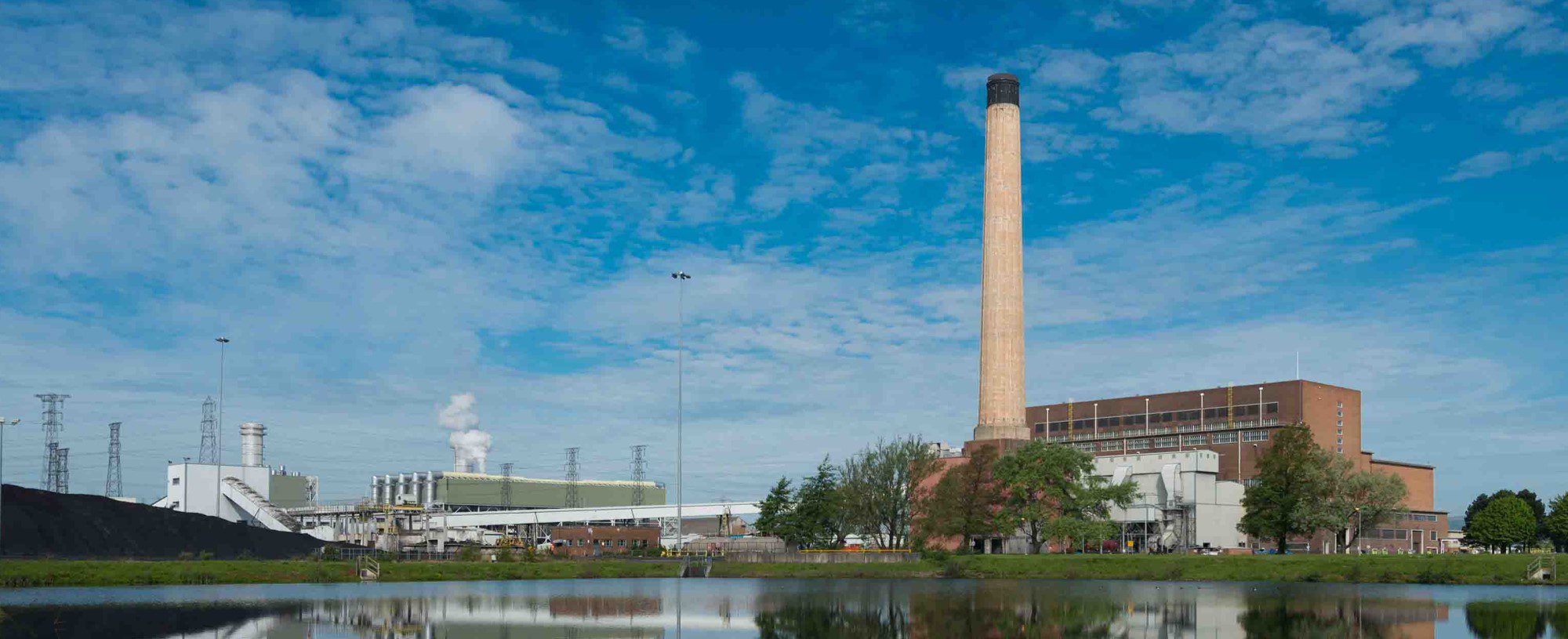
RJM developed a “new generation” energy pellet, simulated the combustion process with CFD modelling, designed a new burner, and achieved a stable flame
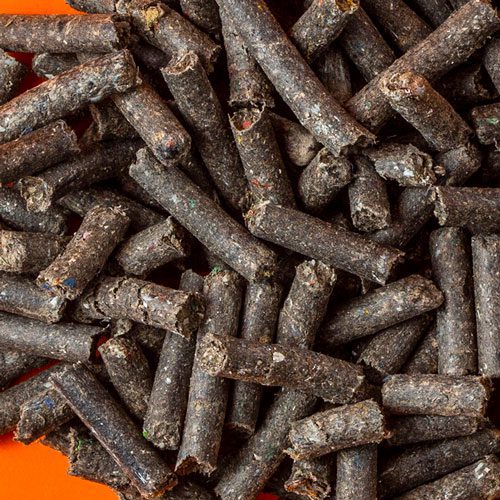
The “new generation” energy pellet formulation consists of 50% biogenic material (wood, paper, cloth) and 50% plastic.
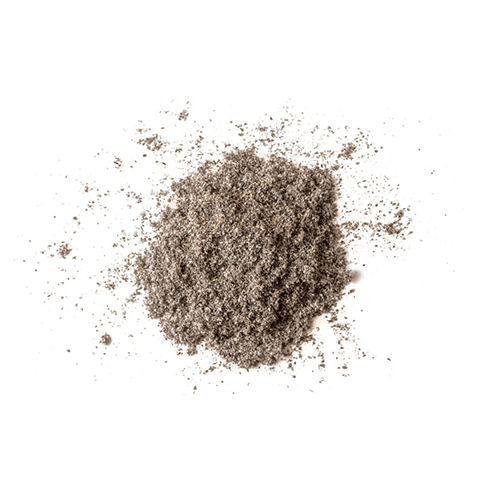
Pulverised pellet prior to combustion.
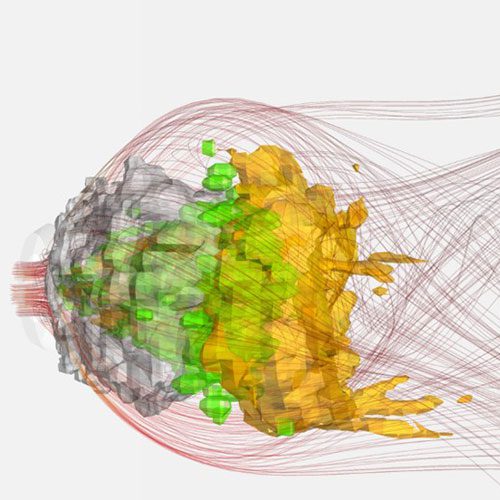
State-of-the-art CFD modelling confirmed that the different constituents of the pellet have different devolatisation and aerodynamic properties.

Achieving a stable, unsupported flame in medium-scale testing was a key success milestone for RJM.
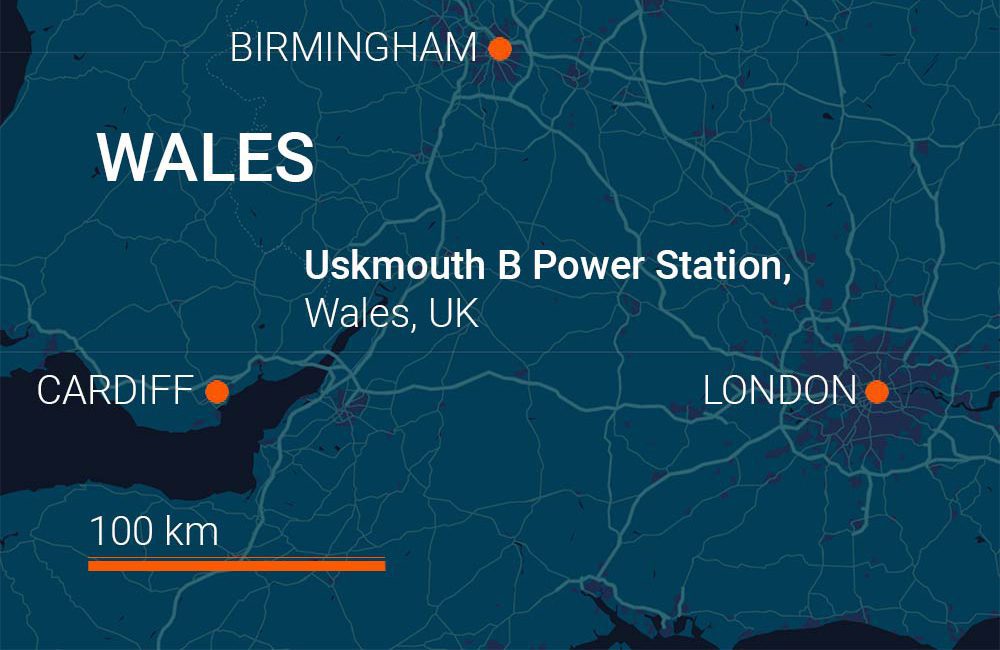
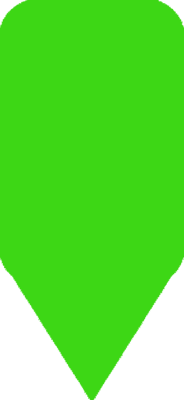
Uskmouth B Power Station, Wales, UK
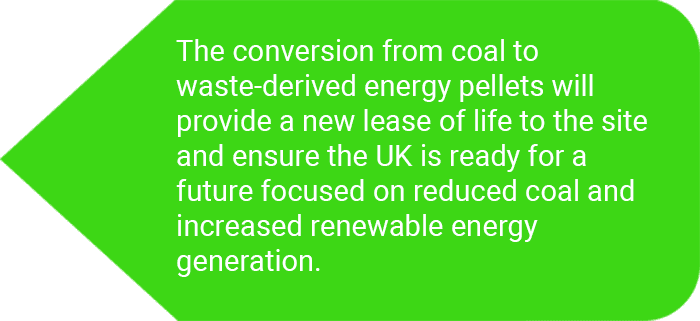
The conversion from coal to waste-derived energy
pellets will provide a new lease of life to the site and
ensure the UK is ready for a future focused on
reduced coal and increased renewable energy
generation.
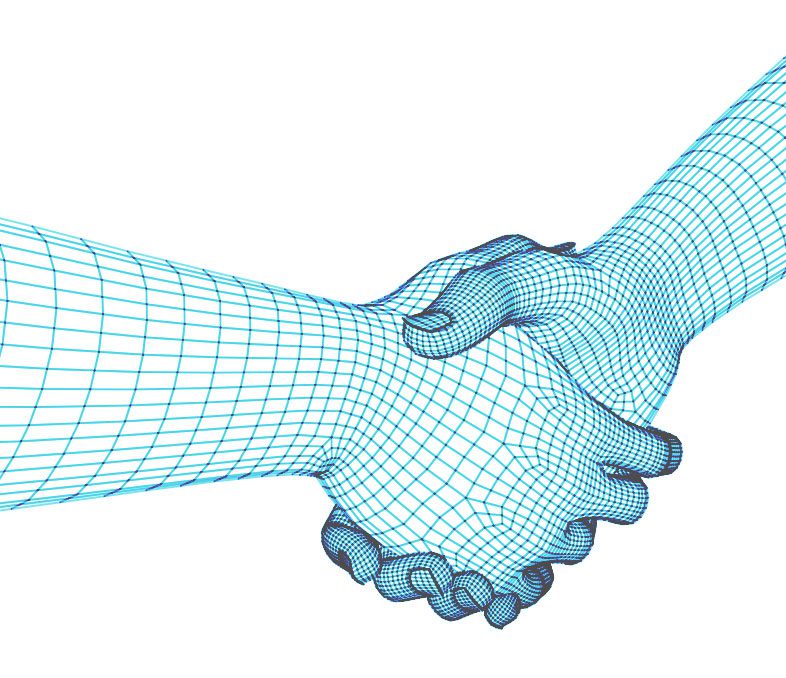
Partnership in action
RJM appointed HKL Global to act as its
agent in the Chinese industrial burner
market in 2016. The two companies have
been working closely together since then,
building up sales of the CleanAir Burner™
within Beijing and now rolling out this unit
into greater China.
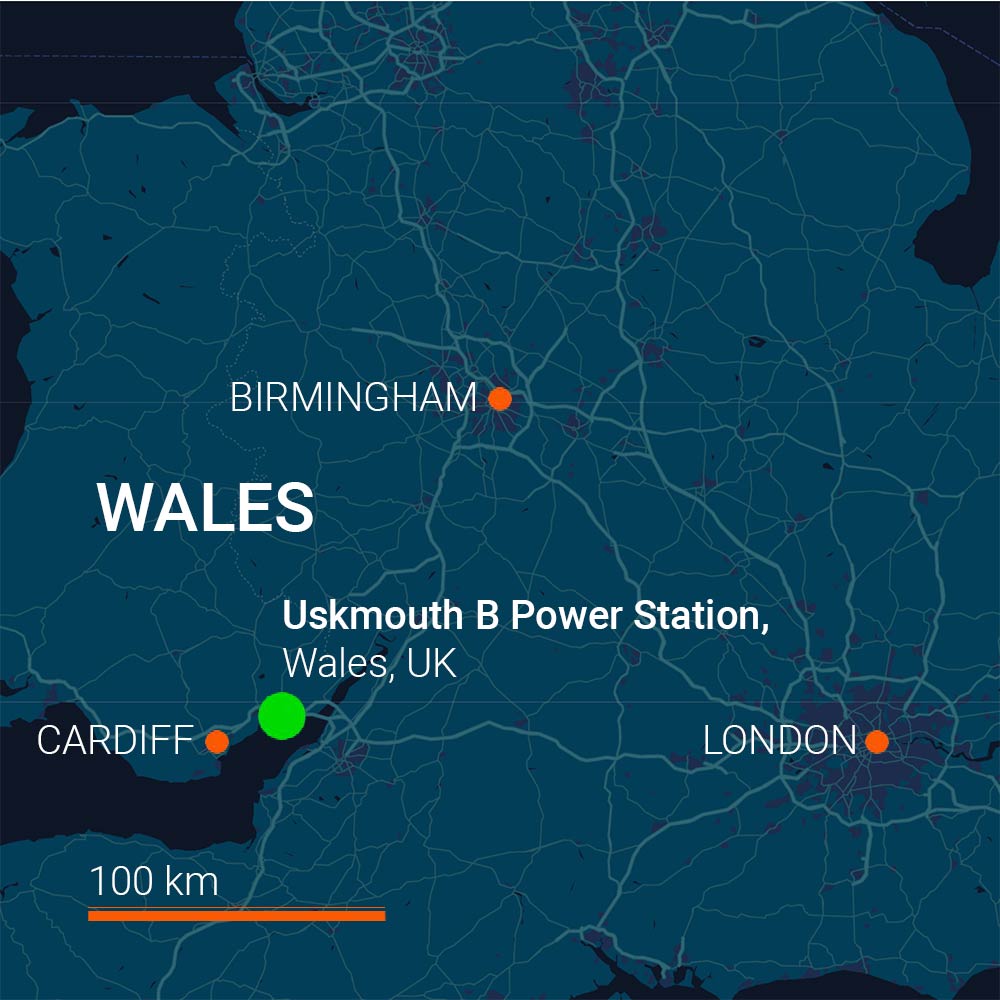
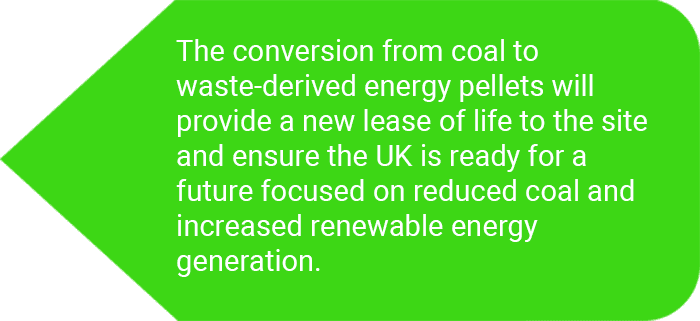
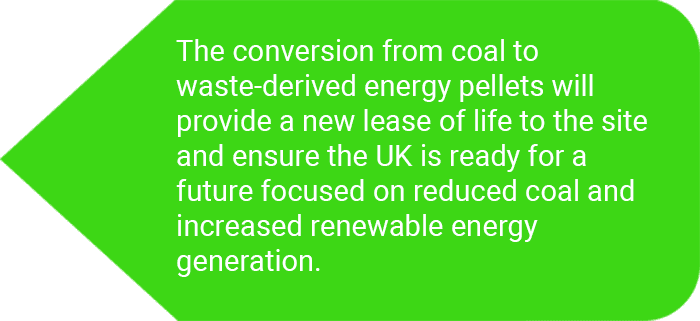
We understand the chemistry of combustion
RJM employs world-leading combustion professionals, with expertise across all boiler types and all fuels, including coal, oil, gas, biomass and Energy from Waste. Our combustion experts are also at the forefront of designing a new generation of low carbon energy pellets and their associated firing systems, including burners, at commercial scale.
Close X
We exploit a range of modelling techniques
Through detailed combustion audits on site, including precise measurement of all the key physical aspects of the plant, RJM’s engineers can build an accurate model of plant performance. This data is then fed into RJM’s own enhanced CFD (Computational Fluid Dynamic) programme so that performance upgrades can be devised, tested and proven. Physical to-scale modelling is also carried out to optimise ducting fuel/air flows whilst DEM (Discrete Element Method) modelling is used to understand the bulk behaviour of different sized elements within granular materials, especially biomass and waste-derived fuels.
Close X
We enable power plants to widen their fuel diet
With the world rapidly moving towards lower carbon generation, RJM is helping power plants assess how they can transition to co-firing, full-scale conversion to biomass fuels, or firing the new generation energy pellet. RJM has completed over 12,500MW of feasibility studies for nine UK and EU power stations plants and has the capability to deliver the entire fuel conversion programme. This capability is now being applied to help biomass and Waste to Energy plants accept new fuels without impacting negatively on emissions, availability or efficiency.
Close X
Delivering reliable energy with at least 50% less carbon emissions
Uskmouth B Power Station is a 363MWe plant. Following the successful completion of the fuel conversion project on two of the three units, totalling 220MWe, it is SIMEC Atlantis Energy’s ambition that this plant will deliver low carbon electricity into the grid.
On this ground-breaking project, RJM has provided:
* Feasibility Study to evaluate conversion to 100% biomass-firing
* Pre-FEED Study
* Full FEED Study
Discover +
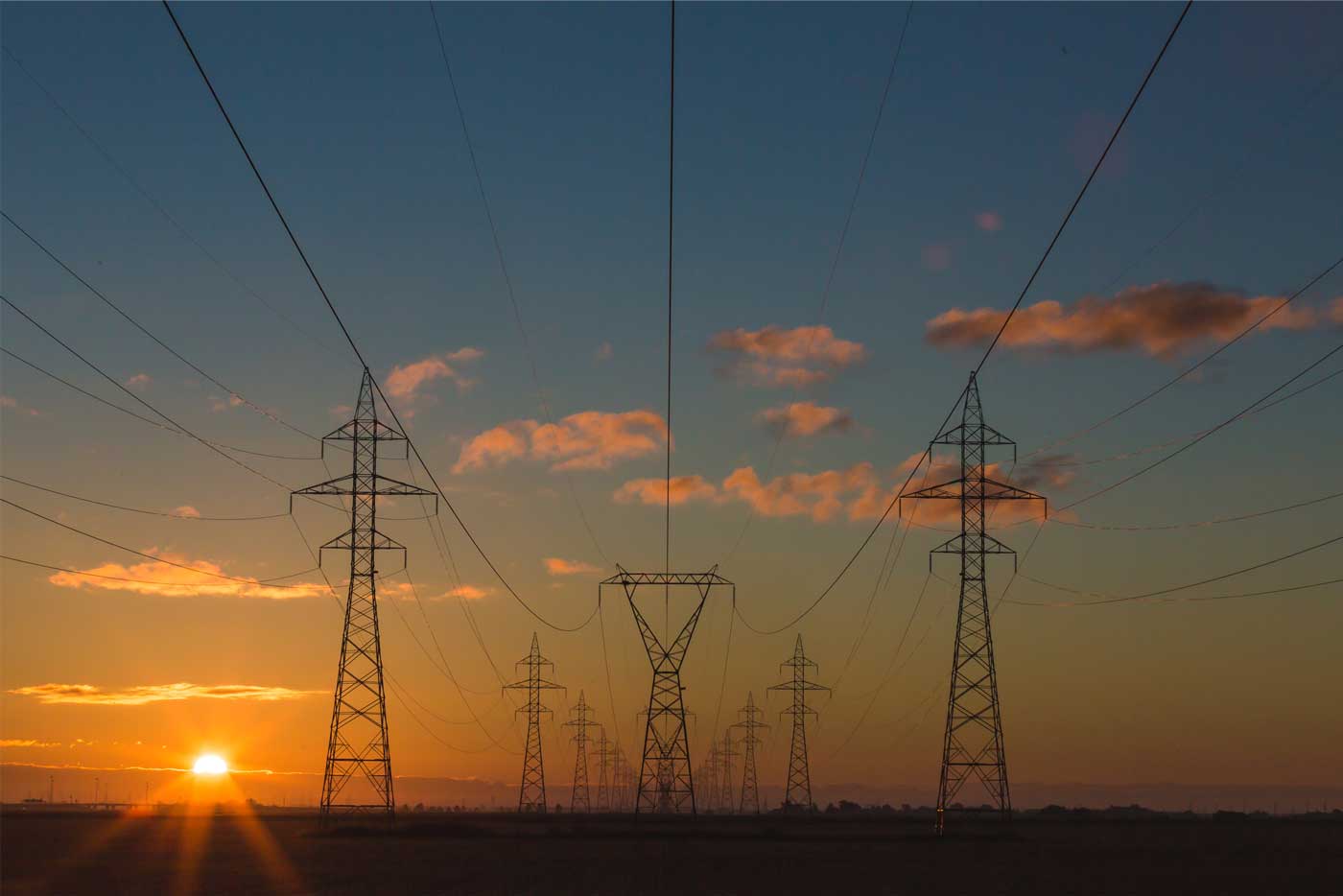
As an award-winning provider of innovative energy and emissions reduction solutions, RJM was first appointed to provide specialist expertise in July 2015 at the inception of this unique conversion project. RJM initially undertook a feasibility study looking at a potential conversion to 100% biomass-firing, before being appointed to carry out a pre-FEED (Front-End Engineering and Design) Study. This led onto RJM being commissioned in November 2018 to carry out the full FEED Study, working in partnership with WSP, one of the world’s leading engineering professional services consulting firms.
In addition, this plant will help the UK tackle the big issues of non-recyclable plastic waste management and baseload energy generation, but that it will also form the basis for the conversion of similar plants worldwide. As an award-winning provider of innovative energy and emissions reduction solutions, RJM was first appointed to provide specialist expertise in July 2015 at the inception of this unique conversion project. RJM initially undertook a feasibility study looking at a potential conversion to 100% biomass-firing, before being appointed to carry out a pre-FEED (Front-End Engineering and Design) Study. This led onto RJM being commissioned in November 2018 to carry out the full FEED Study, working in partnership with WSP, one of the world’s leading engineering professional services consulting firms.
Brave New World
During its work on the FEED Study, RJM tackled a number of new challenges including pellet composition and manufacture; pellet transport and storage; pellet milling and delivery into the furnace. It also carried out detailed financial modelling and CFD analysis to gain a thorough understanding of the chemistry taking place during combustion. This focused on understanding how different elements within the pellet, of different mass, follow individual trajectories as they are fired through the burner, as well as observing how they devolatise at different rates. At medium-scale physical testing, RJM worked closely with a leading European university and carried out an advanced programme of test combustion firings to arrive at a pellet formulation that could maintain a stable, unsupported flame.
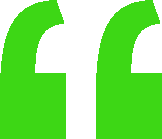
As a business, we are as committed as SIMEC Atlantis Energy, the operator, to using this project as a blueprint for further conversion of similar power plants worldwide to help address the key challenge of how we can treat waste material in an environmentally responsible manner and use it to generate low carbon energy.
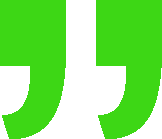
John Goldring,
Managing Director, RJM International
It takes
450 years
for a plastic bottle
to biodegrade
We’ve got a much better
end-of-life use for it!
The energy pellet formulation
consists of 50% biogenic
material (wood, paper, cloth)
and 50% plastic.
As the world transitions towards low-to-zero power generation, there is a real opportunity today for redundant coal-fired assets to be re-tasked to fire this new generation energy pellet. Reliable, affordable, low emissions and crucially low carbon energy is the valuable prize from firing these energy pellets. They can also be deployed to maintain continuity of supply, during the transition period when a combination of more renewables, more energy storage and reduced demand can grow to take on a much more significant share of the energy landscape.
Supporting the 3Rs – Reduce, Reuse, Recycle
RJM’s involvement in the development of the new generation energy pellet to optimise it for firing in PF (Pulverised Fuel) boilers gives a viable new option for tackling our plastics crisis and offers particular advantages in those markets where a sophisticated recycling infrastructure does not yet exist.
Close X
RJM is helping existing Waste to Energy and biomass power plants operate more reliably, efficiently and cleanly
Owners and operators of these plants are frequently facing new challenges as they seek to integrate a wider range of fuels, beyond the original plant design. In addition, they are having to meet tightening emissions limits and satisfy increased demand for plant flexibility, reliability and capacity utilisation.
RJM International has expertise across all firing configurations and all fuel types and can tackle any aspect of plant under-performance. Today, RJM is working for a number of multi-site biomass and Waste to Energy generators in the UK, Europe and the USA, resolving a wide range of complex operational issues across materials handling, fuel combustion and emissions.
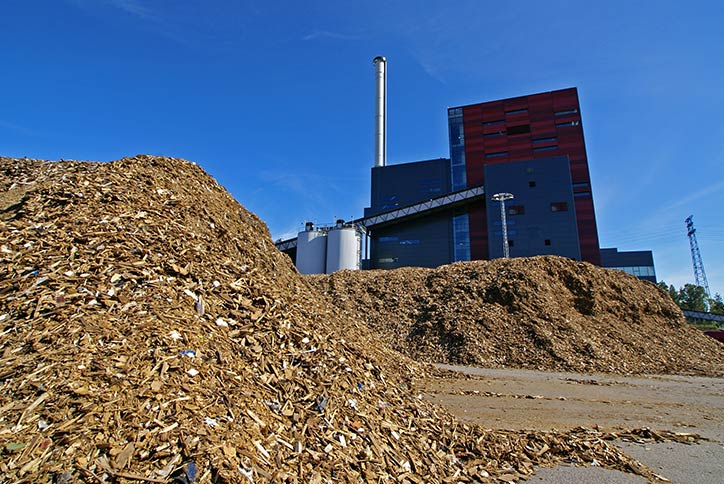
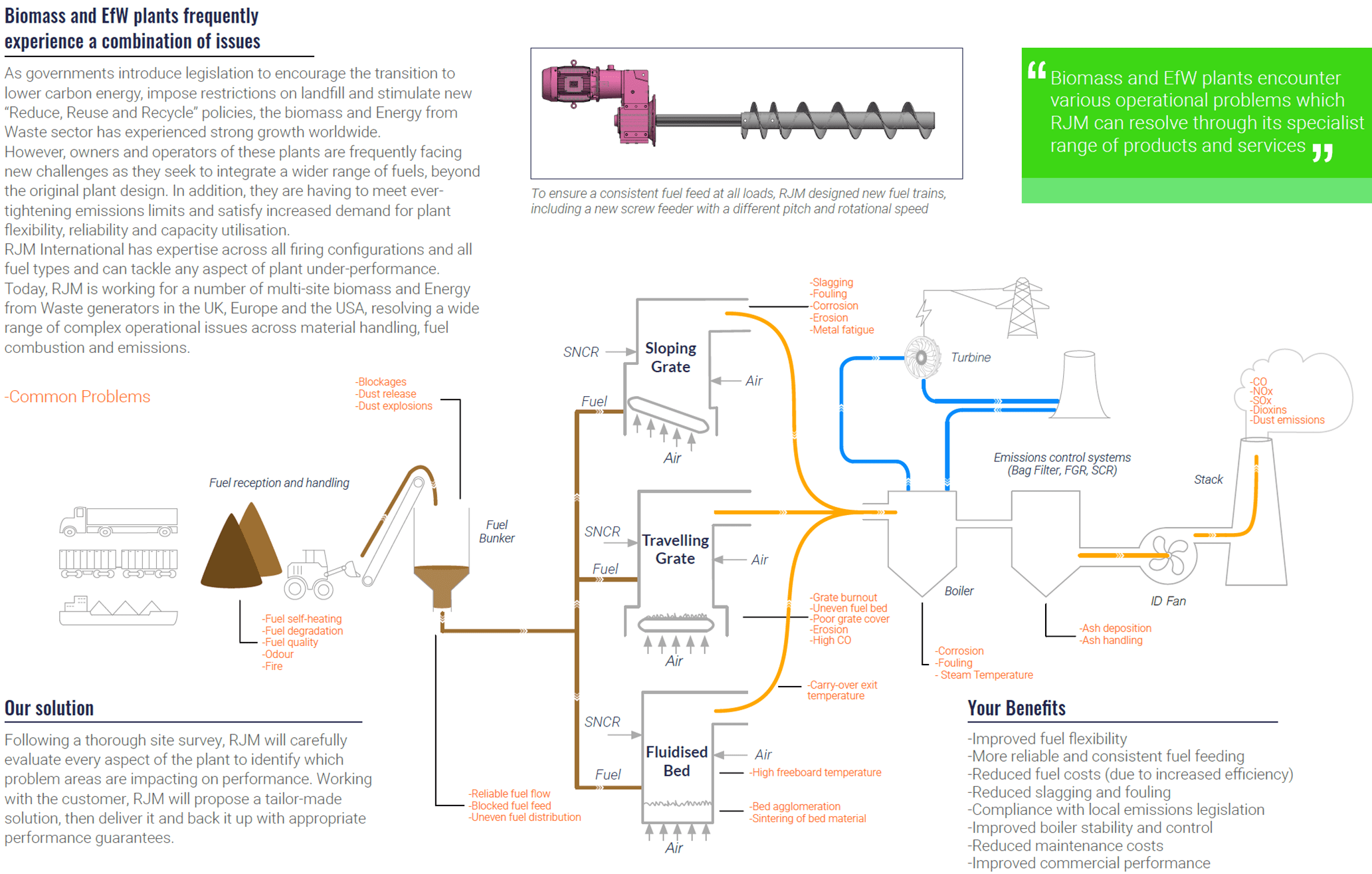
I would like to thank RJM for its support in 2020 which helped us successfully pass the 95% installed capacity test. This enabled Energy Works Hull to qualify for the Contract for Difference subsidy scheme. I believe RJM was instrumental in the screw design, screw speed and fuel feed operation to help us achieve this. I also think the RJM approach of great ideas, designing, modelling and implementing has helped us with this success.
Mark Roberts, Head of Engineering, Bioenergy Infrastructure Group
Explore the reference projects where RJM has provided clients with unique Waste to Energy and Biomass solutions
Site survey and CFD model to design NOx control solution
England
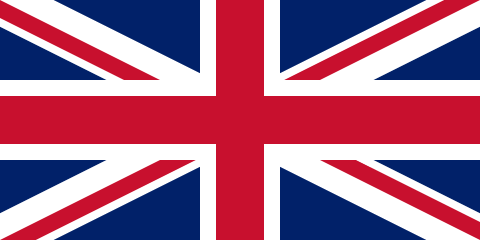
Tradebe, Fawley
Key challenges
This rotary kiln firing system processes a range of hazardous and medical waste streams and the plant operator initially tasked RJM to carry out at NOx abatement study.
Modelling of post-combustion flue gases to increase residence time
Wales
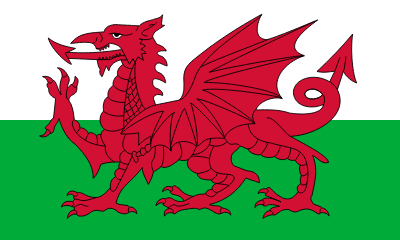
Tradebe, Wrexham
Key challenges
This grate furnace incineration plant firing bio-waste needed to ensure that the residence time of the flue gases was in excess of two seconds at 850 degrees C in order to meet the Waste Incineration Directive that regulates emissions of dioxins and furans.
Full programme of works to improve reliability and operational performance
England
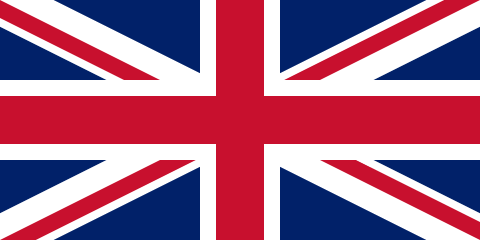
Ince Bio Power
Key challenges
The plant was experiencing a number of operational factors that impacted negatively on performance, including excessive slagging, fouling and corrosion.
Detailed plant review to identify root causes of operational under-performance
England
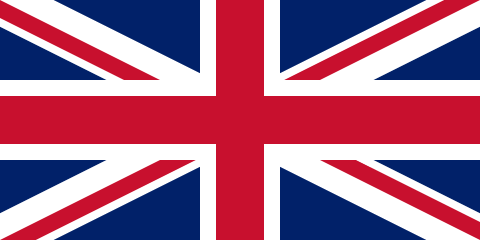
Templeborough Biomass Plant
Key challenges
This plant, having been recently acquired by Greencoat Capital, one of Europe’s largest renewables investors, was experiencing a number of operational issues. RJM was tasked by the new owner with determining their root causes. Key issues were around the reliability and robustness of the grate, severe fouling in the economiser and whether or not the waste wood fuel, or the design of the plant were contributory factors.